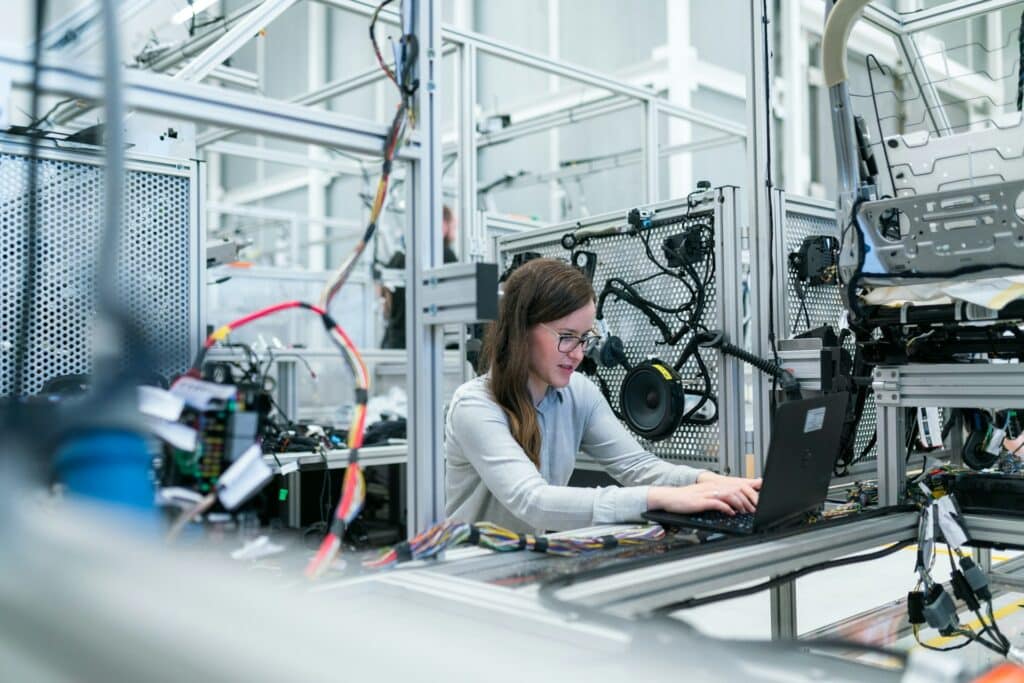
Sage Intacct provides manufacturers with a modern accounting system built in the cloud and equipped with innovative features, including multidimensional reporting, AI-powered general ledger (GL) and more. With the new Sage for Distribution and Manufacturing Operations (SDMO) integration, you will be able to connect your financial management with all of your supply chain operations from inventory tracking to production scheduling. Leveraging this combined ecosystem of solutions grants you end-to-end operational automation and visibility, empowering your team to significantly the time – and costs – it takes to complete each task and consolidate your processes within as few software applications as possible.
Here are the top reasons why Sage Intacct integrated with SDMO is the future of manufacturing operation management:
Sage Intacct – Comprehensive Accounting Software Ecosystem
ERP and other accounting systems provide insight into your financial silos through granular reporting features, with true enterprise-level solutions able to connect to data flows in your operations to give you a 360-degree view of your business. The ability to capture this expanded visibility makes such software critical for building a technology stack where each application works together seamlessly, enabling information to be shared in real-time between teams (when hosted in a cloud server).
As a native SaaS accounting software that features a wide collection of API connectors, Sage Intacct delivers both robust financial management capabilities as well as easy integration with many of the top best-of-breed systems on the market – here are some of the top features available in this solution:
- Dimensional Accounting: Enhances reporting flexibility without the need for extensive account codes
- Artificial Intelligence: Automates bookkeeping and time tracking, with capabilities for anomaly detection and quick data adjustment
- Dashboards: Provides consolidated views of key performance indicators with detailed access control
- Report Designer: Allows for intuitive and flexible report customization and detailed dimensional analysis
- Process Maps: Visual tools to help navigate operations more easily
- Multi-Entity Accounting: Manages multiple entities within one system, supporting various currencies and regulations
- Intelligent GLtm: Offers a sophisticated general ledger system with customizable fields and real-time data visibility
- Accounts Payable/Receivable: Integrates payment processing for streamlined transactions
- Cash Management: Delivers comprehensive insights into cash flow and automated bank reconciliation
- Order Management: Integrates order processing with other financial systems for efficiency
- Purchasing: Speeds up purchasing workflows with automated systems and performance tracking
The Significance of Integrated Systems for Modern Manufacturing
In a modern manufacturing supply chain for SMBs and midmarket enterprises, multiple systems are often needed to help streamline, automate and even just keep track of all of the moving parts from pre-production to end product to transportation. Software ROI is captured from being able to consolidate as many of these activities as possible without losing efficiency or effectiveness, which is why seamless integration between your critical applications is key. You can implement a number of cheap solutions at all of your sites, but if they do not communicate with each other and users are running around plugging in data manually, then how much money – and time – did you truly save?
Sage Intacct Marketplace for Integrations
Sage Intacct is designed to be purpose-driven and ensure that it works in conjunction with the rest of your software ecosystem as seamlessly as possible, with a cloud API built for flexibility and real-time connection with over 300 third-party apps. Its marketplace of approved partners includes solutions for accounts payable, payroll, project management, CRM, document management, tax automation, expense tracking and more.
Exploring Sage for Manufacturing Operations Integration
SDMO is the key internal integration developed for manufacturers using Sage Intacct, bridging the gap between your financial, distribution and manufacturing silos and delivering one source of truth for your supply chain operations. It provides built-in workflow automations for procurement and requisition tracking, material tracking, resource tracking and scheduling, inventory and warehouse management, labor tracking, kit assembly, forecasting, order fulfillment and processing, business intelligence and reporting, and much more.
Sage Intacct Manufacturing and Distribution Features
Besides the core financial management solution, Sage Intacct provides users with several additional modules for function-specific use cases like Planning and Budgeting or industry-specific features such as with Sage Construction Management or Sage Intacct Inventory. With the Sage Distribution and Manufacturing Operations module, you gain a streamlined ecosystem allowing you to handle production planning and capture end-to-end traceability from every point in your value chain, delivering 360-degree visibility for all of your process and empowering your regulatory compliance.
Key Features of SDMO for Sage Intacct
Category | Feature | Description |
---|---|---|
Setup | Setting up Items in Manufacturing | Includes defining item statuses, manufacturing checkboxes, lot/serial management, and production lead times. |
Manufacturing Sites | Select the Manufacturing option on the Management tab for site definition to enter work orders, bill of materials, routings, etc. | |
Designing | Bill of Materials (BOM) | Allows creation and management of hierarchical lists of components needed to manufacture products, including cost calculations and material requirements planning. |
Resources (Labor, Machine, Tool) | Setup for defining labor, machines, and tools used in manufacturing, along with their capabilities and efficiency. | |
Routings | Defines the sequence of operations required to build a product, detailing the resources and instructions needed for each step. | |
Work Orders & Tracking | Work Orders | Management of documents that authorize the manufacture of goods, including linking to BOMs and routings, and tracking material and time usage. |
Material Tracking | Tracks the actual quantity of components issued from stock and consumed in the production process. | |
Time Tracking | Monitors the time taken by resources to perform operations, affecting the cost calculations of the production. | |
Production Tracking | Allows for receiving finished items from production, including backflushing operations and tracking production costs. | |
Inquiries and Reports | Work in Progress Inquiry | Enables inquiries into ongoing work, including tracking of work orders and production progress. |
Material and Time Tracking Inquiries | Provides detailed tracking of material issues and time recording for manufacturing operations. |
Competitive Landscape for Manufacturing Accounting Software
Compare Sage Intacct against other ERP solutions in the manufacturing and see how it holds up against other leading accounting software:
Sage Intacct vs Microsoft Dynamics SL
- Sage Intacct automates critical financial processes, reducing dependency on manual spreadsheets and enhancing real-time business performance visibility. Its ability to connect with various third-party systems streamlines integrated data flows, contrasting with Dynamics SL’s more limited integration capabilities.
- Modern cloud accounting software provides a high level of security and operational efficiency, often at a lower cost than legacy ERP systems like Microsoft Dynamics SL.
Sage Intacct vs SAP Business One
- Sage Intacct offers greater scalability suitable for a wide range of business sizes. Conversely, SAP B1 targets smaller business segments and requires costly upgrades for additional functionality due to its origin as an on-premise solution.
- Sage Intacct provides a more user-friendly interface with customizable dashboards and dimension-based reporting. SAP Business One often requires additional layers of customization.
Sage Intacct vs NetSuite
- Sage Intacct offers a more cost-effective cloud subscription model without locked-in contracts, providing flexibility in scaling as business needs change. In contrast, NetSuite tends to be more expensive over time with a tiered pricing model that might include upfront costs and additional fees for advanced features.
- Sage Intacct is purpose-built as a state-of-the-art accounting solution first and foremost, excelling in financial management with an AI-powered general ledger and deep reporting features that can filtered as granularly as you need. NetSuite on the other hand offers a wide breadth of functionality for various industries but much less depth.
Sage Intacct vs Other Sage Software for Manufacturing
Comparing Sage Intacct with other Sage ERP for manufacturing? Review the comparison points below:
Sage Intacct vs Sage 100
- Sage 100, though cloud-connected, does not fully feature true SaaS capabilities and instead relies on hosting options with either a certified provider or Sage Partner Cloud. Sage Intacct’s cloud-native platform enhances productivity with real-time updates and unlimited multi-tenant scalability.
- Sage Intacct also integrates seamlessly with best-of-breed applications like Salesforce or Procore for extensive automation capabilities.
Sage Intacct vs Sage 300
- Sage Intacct provides superior financial management tools than Sage 300, including granular multi-dimensional reporting, real-time analytics, and multi-entity consolidation capabilities. These features are particularly beneficial for businesses that require detailed accounting insights and efficient handling of complex bookkeeping processes across multiple business units.
- Sage Intacct excels in seamless integration with other applications and offers extensive in-app customization options, enhancing overall business operations efficiency. Sage 300 also supports some integrations and allows for customization, but these generally involve more complexity as well as additional costs due to its traditional ERP framework.
Sage Intacct vs Sage X3
- Sage Intacct is a cloud-native solution, offering advantages in scalability and remote access without the need for extensive setup. Sage X3, although it supports cloud functionality, typically needs additional infrastructure and third-party services to become full-remotely operational.
- Sage Intacct provides greater flexibility in customization and integration with other applications, facilitating streamlined workflows and enhanced data insights. Sage X3, while customizable, often requires more complex modifications to meet specific business needs.
Learn More About Sage Intacct for Manufacturing Operations
Get in touch with SWK Technologies today to see for yourself how SDMO integrated with Sage Intacct will take your manufacturing operations into the future. Our team of experts will show you firsthand all the benefits of this connected accounting software ecosystem and leverage our decades of experience customizing Sage software for manufacturers to ensure you get the most out of your technology.
Contact SWK here to learn more about Sage Intacct’s manufacturing capabilities and discover how to take advantage of it for your operations.