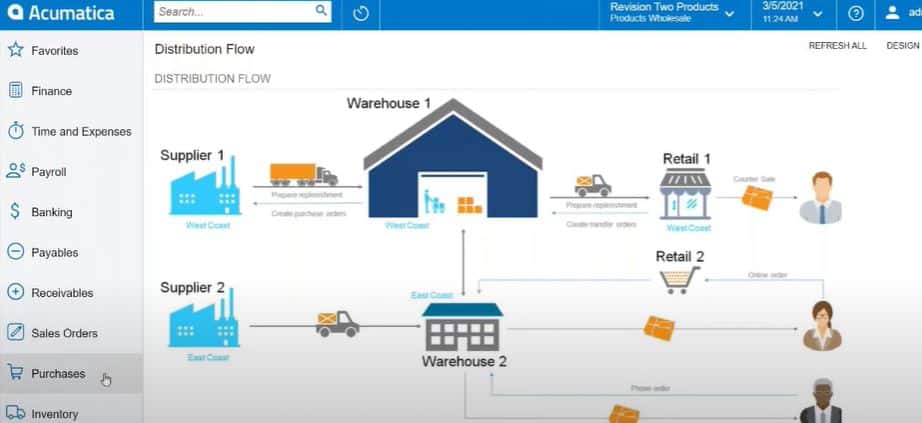
This demo of Acumatica Distribution Edition will dive deep into the various features available that allow you to accelerate your processes and automate tedious, repetitive tasks, as well as capture end-to-end insight into your supply chain at all stages. With intricate inventory management controls, vendor and warehouse management automations, and integrated shipping and fulfillment capabilities, this cloud ERP empowers distributors to streamline operations without bouncing between multiple applications and screens.
Watch the video version here, or keep reading below to see the detailed demonstration:
Acumatica Distribution Management Walkthrough
The Acumatica Distribution Suite is a comprehensive solution for managing inventory, quotes, sales orders, purchase orders, returns, and requisitions. The Distribution suite is fully integrated with other Acumatica modules, such as Accounts Receivable (AR), Accounts Payable (AP), General Ledger (GL), Customer Relationship Management (CRM), and Fixed Assets.
Inventory Management
I begin by navigating to the Distribution tab in Inventory. You can manage both stock and non-stock items within Acumatica as well as kits that include component items.
Each item has a master inventory record that includes:
- Item Classes: Categories like consumer goods or food items for reporting purposes
- Lot and Serial Classes: Rules for automatic lot and serial number assignments
- Valuation Methods: Methods such as average cost, standard cost, or FIFO (First In, First Out) to accurately reflect the cost of goods
- Units of Measure: Conversion capabilities based on the units in which items are purchased versus sold
- Price and Cost Information: Details regarding pricing, costs, warehouse specifics, vendor information, and additional attributes like color or size
Item Configuration
From the general settings tab, you can configure various aspects of your inventory:
- Item classes (e.g., consumer goods or food items) for reporting purposes
- Lot and serial classes to set rules for automatic lot and serial number assignment
- Valuation methods (e.g., average, standard, or FIFO) to accurately reflect the cost of goods on your books
- Units of measure that can be converted based on selling and purchasing units
You can also manage:
- Price and cost information
- Warehouse details
- Vendor details
- Attributes like color or size
Replenishment Settings
Set replenishment information for your items to dictate reorder points. For example, you can specify that when stock levels drop below 10 units, a purchase suggestion should be sent to your supply chain manager.
Purchase Order Management
Purchase Suggestions
The dashboard for supply chain or shipping and inventory managers displays purchase suggestions based on preset reorder points. From here, you can:
- Drill into purchase suggestions to begin the replenishment process
- Manually enter a purchase order
- Use the system’s suggestions for items and vendors
- Process and prepare for replenishment
Creating Purchase Orders
You have the option to manually enter a purchase order or use the system’s suggestions for items and vendors. The “Create Purchase Orders” screen automatically prepares purchase orders ready for replenishment, allowing you to confirm default vendors and quantities before processing.
Vendor Communication
Once processed, purchase orders can be emailed to vendors. These emails appear in the activity log of the PO record and can be customized to fit your organization’s needs.
Receiving Inventory
After the lead time has passed, you can enter the purchase receipt, updating on-hand and available inventory numbers in real-time.
Automation
Acumatica offers the ability to set automation schedules for purchase orders, allowing the system to create them behind the scenes automatically. You can set conditions and specify dates and times for these schedules to run.
Sales Order Management
Creating Sales Orders
When creating a sales order:
- Select a customer, and their financial settings (terms, discounts) will be auto-applied
- Add line items manually or use the “add stock item” button
- Review the customer’s order and price history
Order History and Pricing
Acumatica allows you to view a customer’s order history and price history over time, helping you make informed decisions when adding items to an order.
Shipping Integration
The system offers integrated carrier rate shopping, allowing you to compare and select the most suitable shipping option for each order.
Warehouse and Shipping Operations
Order Fulfillment
Warehouse employees can access sales orders ready for shipment directly from their dashboard. The process includes:
- Creating a shipment
- Printing pick lists (which include barcodes for scanning devices)
- Confirming the shipment
- Generating shipping labels
Shipping Documentation
Once the order is picked and the shipment confirmed, you can print shipping labels directly from the system.
Financial Integration
After order fulfillment, the finance team can prepare and email invoices to customers. These invoices are then released to the General Ledger, providing all associated batch information for accurate financial tracking.
Discover More Tips, Tricks and Other Features for Acumatica
SWK Technologies will help you get the most out of your ERP investment, leveraging our deep technological and industry knowledge as a top Acumatica partner and Community resource. Check out some of our Acumatica videos and other educational resources, and reach out to us when you’re ready to learn more tips and tricks to maximize your value return on your software.
Contact SWK here to gain access to more Acumatica tips, tricks, updates, and tailored demos.