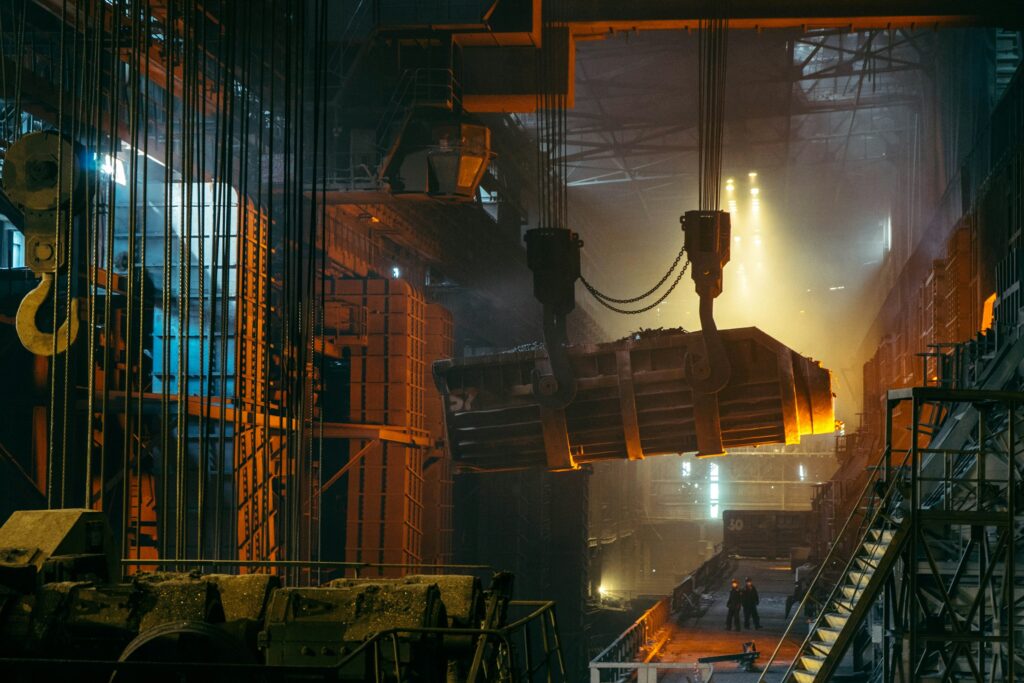
Acumatica Manufacturing Edition provides an end-to-end suite of production and supply chain management tools as well as supporting applications. This comprehensive ERP delivers solutions for manufacturers in various vertical channels, including make-to-stock, make-to-order, engineer-to-order, project-centric, job shop, repetitive and batch manufacturing.
These video resources from SWK Technologies demonstrate the core applications that make up this suite, which will be broken down further below:
Acumatica Manufacturing Edition Modules
The Manufacturing Edition suite in Acumatica Cloud ERP consists of several primary modules, including:
- Bill of Material (BOM) and Routing
- Production Management
- Material Requirements Planning (MRP)
- Manufacturing Estimates
- Advanced Planning and Scheduling (APS)
- Engineering Change Control (ECC)
- Customer Management (Acumatica CRM)
Bill of Materials (BOM) Module
The Bill of Materials module is the foundation for planning functionality throughout the system. It creates production specifications and offers the following features:
- Integrated BOM and routing with direct connection of materials, work instructions, and overhead costs to labor operations
- Effectivity and expiration dates for phase-in and phase-out of content changes
- Phantom items for simplified structure maintenance
- Reference designators to relate BOM components to drawing part numbers
- Multiple site management with different BOM/Routing definitions for each location
- Flexible BOM cost roll activities for single or multi-level BOMs
- Mass change functionality for component replacements
- Attribute management for optional or required values in production reporting
- Revision control with complete history
Production Management Module
The Production Management module gives you control over the entire production run from scheduling to minute order management. Key features include:
- Creation of production orders from BOMs, sales orders, or MRP
- Real-time tracking of material, labor, machine, and overhead costs
- Critical materials management
- Labor and material tracking with backflushing capabilities
- Lot and serial number tracking throughout the item lifecycle
- Barcode integration for data collection
- Multi-site support
- Outside processing alignment with purchase orders
- Pre-assignment of lot/serial numbers for finished goods
- Real-time production dashboards
- Multi-currency support
- Cost accounting controls with production order lock status
- Non-sequential production reporting
- Event audit trail for all production activities
Production Order Details
When a production order is created, the entire BOM and routing is copied to the production order details, showing:
- Product structure
- Start and end dates
- Status
- Quantities completed and scrapped
- Labor costs
- Material issued and actual material costs for each operation
Production Order Statuses
Production orders can have seven different statuses:
- Planned (default for new orders)
- Released
- In Process
- Hold
- Completed
- Cancelled
- Closed
Scheduling Methods
The system supports multiple scheduling methods:
- Finish On: Backward schedules from a specific completion date
- Start On: Forward schedules from a specific start date
- ASAP: Forward schedules starting today
- User Dates: Allows manual definition of start and end dates
Material Requirements Planning (MRP) Module
The MRP module is a crucial planning tool that helps your business balance supply and demand while maintaining optimal inventory levels. Key features include:
- Time-phased material planning
- Integration with Master Production Schedule (MPS)
- Full regeneration capabilities
- Forecasting tools with manual and calculated options
- Multi-warehouse management
- Queue, finish, and move time definitions
- Grace period settings
- Exception management
- Demand time fence specifications
- Transfer order management
- Blanket sales order support
- Customizable order quantities and lead times
- MRP history and audit functionality
- Kit and component planning
- Configurable RMA options for inventory planning
Manufacturing Estimating Module
The Estimating module in the Manufacturing Edition offers a streamlined approach for creating estimates for new items, integrating with Acumatica CRM, and converting estimates into production orders. Other features include:
- Multi-quantity estimate worksheets
- Estimation for non-inventory items
- Easy conversion of estimates to inventory items and BOMs
- Direct creation of production orders from estimates
- Flexible mark-up options for materials, labor, overhead, and tooling
- Integration with your CRM and sales workflows
- Multi-site estimate creation
- Optional CAD connectors for BOM and routing creation from engineering drawings
- Estimate insights through dashboards and reports
Product Configuration Module
The Product Configurator module provides flexibility to define attributes and formulas to create unique bills of material and routings for finished goods with calculated costs and pricing. Key features include:
- Rules-based product configuration
- Creation of formulas for calculated quantities and costs
- Configuration of products for quotes, sales orders, and production
- Support for configure-to-order and configure-to-stock scenarios
- Dimensional capability for material requirements calculations
- Order history lookup for quick reference to previous configurations
- Integration with CRM opportunities
- Configuration details printing on invoices
- Configuration endpoints for external application integration
Advanced Planning and Scheduling (APS) Module
The APS module allows manufacturers to consistently and cost-effectively meet customer demands by setting accurate and reliable delivery dates based on finite resource availability. Key features include:
- Finite and infinite capacity scheduling
- Rough-cut capacity planning (RCCP)
- Capable-to-Promise (CTP) functionality
- Visual scheduling board
- Resource capacity planning for work centers, machines, tools, and labor
- Dispatch lists for clear views of scheduled production orders
- Scheduling utilities with filters and color-coding
- Queue, finish, and move time definitions
- Real-time insights through dashboards and notifications
Engineering Change Control (ECC) Module
The Engineering Change Control module in Acumatica Cloud ERP allows manufacturers to manage complex changes to BOMs with strict revision control. Key features include:
- Management of Engineering Change Requests (ECRs) and Engineering Change Orders (ECOs)
- Automated approval workflows for requests and change orders
- Engineering Workbench for interactive BOM creation and modification
- Security controls and audit logs for change tracking
- Engineering dashboard for real-time insights
- BOM comparison tools
- Optional integration with Arena PLM and CAD applications
Customer Relationship Management (CRM) Integration
Acumatica Customer Management delivers an embedded CRM solution integrated with your accounting and content management, as well as with connected Editions such as Manufacturing, Distribution and more. Key features include:
- Unified ERP and CRM data and processes
- Lead and opportunity management
- Account and contact management
- Email management with branded templates
- Task management and automated workflows
- Campaign management tools
- Document management integration
Acumatica Mobile ERP App
The Acumatica mobile app provides remote access to your ERP functions and data on iOS and Android devices. Key features available include:
- Time and expense reporting
- Approvals management
- Task management
- Image upload and signature capture
- Personalized mobile workspaces
- Sales mobility for customer and prospect management
- Construction and service mobility for field operations
- Warehouse and manufacturing functionality for inventory and production management
Demo: Acme Cabinet Company Case Study
To illustrate how this ERP suite works in practice, this video demonstrates how an example company could leverage Acumatica Manufacturing Edition:
Acme Cabinet Company is a furniture manufacturer making both stock and custom cabinets. They are expanding into a new market and need to adjust their production to account for customers who need minor changes to standard models. Here is an example workflow to demonstrate how Acumatica would support this growth strategy:
- Product Configuration: Sales uses the CRM module to review customer needs and provide product configurations such as trim, finish, and hardware for a previously-built standard model vanity
- Inventory Management: The Inventory Management module resolves allocations and substitutions for new components (like popular hinges) and automatically updates bills of material and routings
- Advanced Planning and Scheduling: The plant manager goes into the APS module and schedules the custom order for the second shift to meet the tight deadline
- Mobile Access: The foreman confirms order completion via a tablet leveraging the Acumatica mobile app
- Warehouse Management: From Acumatica WMS (warehouse management system), the finished vanity is moved to a will-call location for customer pickup
- Field Service Management: When an issue arises post-installation, a field technician receives a service order on her mobile device – complete with damage photos sent by the contractor – and enters the estimated repair time and materials required
- Real-time Financial Management: The Accounting department can quickly review actual costs and confirm profit margins for the vanity
Acumatica 2024 Releases – Updates for Manufacturing Edition
Acumatica 2024 R1 and R2 – two major feature releases part of a regular biannual rollout – added several updates for the Manufacturing Edition, including:
Enhanced Estimating
- Accurate cost variations reflecting order quantities and subcontracting costs
- New Price Breaks tab for managing quantity-based pricing
- Optional rounding of unit prices to nearest whole currency unit
- Streamlined Quick Estimate integration with CRM
Production Order Management
- New Related Production tab showing complete parent-child relationships
- Intelligent numbering system with automatic suffixing for subassembly orders
- Expanded subassembly order generation across multiple forms
- Enhanced finite production scheduling considering order dependencies
Project Integration and Inventory Tracking
- Enhanced project-specific inventory tracking in production orders
- New quantity tracking columns:
- Qty On Hand for Project
- Qty Short for Project
- Available Qty for Project
- Refined material planning for project-specific inventory
Outside Processing and Purchasing Integration
- Automated move transactions upon purchase order receipt
- New ‘Purchase and Move’ subcontract source option
- Improved production demand visibility in purchase orders
- Synchronized purchase order dates with material requirements
Production Performance Reporting
- Detailed tracking of labor hours, costs, and overhead by operation
- Comprehensive sections for:
- Subcontracts and materials
- Transaction details
- Sales order production totals
- Enhanced production cost analysis and tracking
Acumatica Process Manufacturing
Acumatica Manufacturing Edition comes with several native features that deliver value for discrete manufacturers in different sectors; the solution can also be tailored for process manufacturing use cases via integration with third-party applications, such as the Quality Management Suite (QMS) by partner eWorkplace Apps. The QMS module adds new functionality for quality assurance and traceability, including:
Quality Control and Testing
- QC testing for incoming raw materials
- Production quality monitoring
- Inventory quality control
- Shipping quality assurance
- Configurable QC tests with accepted values
- Tolerance specifications
- Sample and recount value tracking
Advanced Quality Management
- Certificate of Analysis (COA) generation
- Non-Conformance Reporting (NCR/Deviations/MRB)
- Corrective Actions and Preventive Actions (CAPA)
- AQL & Sampling routines
- Standards compliance management (ISO, GMP, FDA, etc.)
- Lot-based quality control
- Vendor performance evaluation
- Calibration management
Learn More About What Acumatica Provides for Manufacturers
Acumatica Manufacturing Edition provides you with the core tools you need to streamline your business finances and production operations, unified in a comprehensive system that connects data flows from different teams. Working with SWK Technologies, a 4-time Acumatica Partner of the Year, will give you access to a team of ERP and industry experts that will help you tailor your solution around your specific needs and challenges.
Contact SWK here to see what Acumatica can do for your manufacturing business firsthand, and let our expert consultants arm you with the knowledge and tools you need to excel with this cloud ERP.