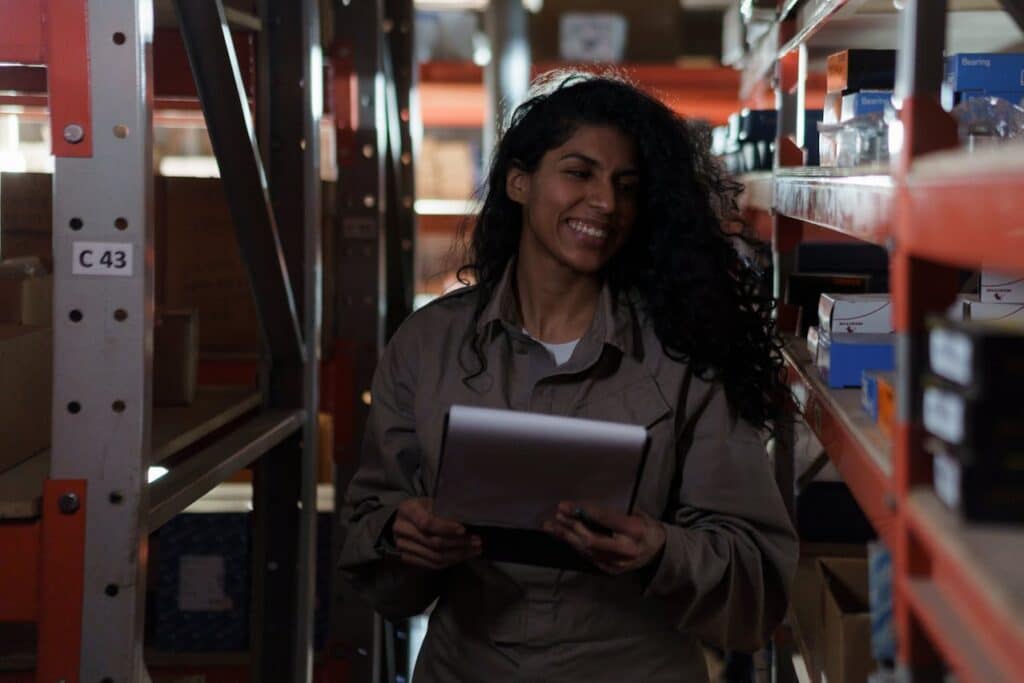
Step-by-Step Guide for Acumatica Inventory Automation
SWK Technologies has put together this comprehensive guide to managing inventory controls in Acumatica Cloud ERP from in-depth training sessions provided to customers. This walkthrough breaks down the features covered and the steps demonstrated for executing tasks in the Inventory Management module available in the Distribution, Manufacturing and Retail-Commerce Editions.
If you are looking for help with a specific issue or have a question not addressed here and are a SWK customer, you can fill out a support form here. If you work with a different Acumatica partner, do not know your reseller or do not have one, or are still just learning more about Acumatica Cloud ERP, then you can contact SWK here.
Acumatica Inventory Management Settings
One of the foundational aspects of inventory management in Acumatica is the configuration of the module’s default settings to match your workflows, modifying any fields and automations to better meet your needs. This training outlined the steps for setting up and adjusting preferences for each area, including for inventory type, items, transactions and locations. The steps covered in this section include:
- Transaction Numbering: Configurable numbering schemes for various transactions, such as receipts, issues, and adjustments, all of which can be managed and customized manually in Acumatica.
- Inventory Preferences: Settings such as managing back orders and allocation rules for documents on hold, offering flexibility in how inventory is accounted for and managed. Important to note here is how Acumatica defines back orders differently than in other systems, including any unfulfilled sales orders automatically rather than only past due items.
- Posting Settings: Various fields control how and where transactions are posted, letting users automate data entry en masse or keep ‘one-off’ activities requiring manual sign-off. The “Update GL” setting is also crucial to ensure that inventory transactions generate corresponding general ledger entries.
Advanced Features in Acumatica WMS
The session highlighted Acumatica’s capabilities for managing different complex warehouse operations, including using multiple warehouses across more than one location, generating wave or batch pick lists, automatically assigning shipping labels and tracking stock by lot, barcode or another internally-assigned definition. Features of note in this section include:
- Acumatica WMS Settings: Insights into the details of Acumatica WMS (warehouse management system) configurations, such as assigning default locations for receipts and issues.
- Default Warehouses: Acumatica Cloud ERP allows you to assign a default warehouse to a user profile, meaning that the system will automatically generate tasks and reports for that user from their assigned warehouse.
- Receiving and Packing: Various default fields that let users automatically or manually enter where received items go once they are scanned, generating different codes that ensure packers and pickers know where each piece of inventory is and where it needs to be at any given time depending on its categorization.
- Multi-Warehouse Support: Exploring the multi-warehouse functionality in Acumatica, including assigning an ID, location or description to each warehouse and branch, and allowing shipments and inventory to be automatically allocated on each report to a given location by default.
- WMS automation in Acumatica lets you map out workflows for picking, packing, putting away and more by applying IDs, codes, lot, serial or other number designations to each piece of the supply chain puzzle, from stock and warehouse to customer or vendor. However, it is critical to walk through the templates and default settings with your consultant or developer and your team before go-live to ensure these are modified correctly for your needs.
- Multi-Tenant Warehouse Reporting: As a cloud ERP, Acumatica has the ability to host data in multiple tenants with specific features, databases and an assigned warehouse location in this case, as the customer required a separate warehouse for a specific company division. SWK Technologies can help you set up and customize each individual tenant for each warehouse or branch, as well as build out a final workflow to consolidate reports from all tenants at once – you can view an example of this in the Unify Square case study here.
- Location Management: Detailed location settings within warehouses that include designating sales orders, receipts, transfer, assembly and more for each assigned location automatically.
- Warehouse Definition: Location, ID number and description can all be used to designate, search for and track a given warehouse in Acumatica and all of the processes and items mapped to that defined warehouse. Locations can also be marked active or inactive to start or cease this automation.
- Item Transfer: It is important to note the difference between one-step and two-step transfers in Acumatica, where the former immediately moves inventory upon release, and the latter involves an initial transfer followed by a receipt confirmation.
- Costs for each location are recorded and tracked separately in Acumatica Cloud ERP, so the average cost for a given location only applies to that warehouse.
Additional Workflows for Inventory Controls
This section compiles additional workflows and use cases covered in the Acumatica Inventory Management training session. Features covered include:
- Item Class Structure: Stock and non-stock items can be defined as their own class each and assigned as default values to be applied automatically on new reports. Class categories can be organized into a hierarchal structure with a parent-child relationship for each top item class and its subcategories, with virtually unlimited granular depth at your discretion.
- Posting Class Configuration: Posting classes control which GL accounts are used for inventory transactions, with options to set them at the item, warehouse, or posting class level.
- Note that changes to posting classes do not automatically update existing documents. You may need to update or recreate documents to apply new posting class settings.
- Stock Level Calculation: Acumatica allows users to define rules for calculating inventory availability based on various factors such as including quantities on purchase orders, sales orders, or in-transit.
- Inventory Recalculation: Users can recalculate inventory weekly to refresh stock counts in the ERP database.
- You can review historical inventory levels and valuations compared to current reports to help identify and reconcile discrepancies.
- Acumatica Module Integration: Inventory Management integrates and syncs directly with additional modules in Acumatica Cloud ERP, including Sales, Purchasing and Financial Management.
Discover More Tips, Tricks and Other Features for Acumatica
SWK Technologies will help you get the most out of your ERP investment, leveraging our deep technological and industry knowledge as a top Acumatica partner and Community resource. Check out some of our Acumatica videos and other educational resources, and reach out to us when you’re ready to learn more tips and tricks to maximize your value return on your software.
Contact SWK here to gain access to more Acumatica tips, tricks, updates, and tailored demos.