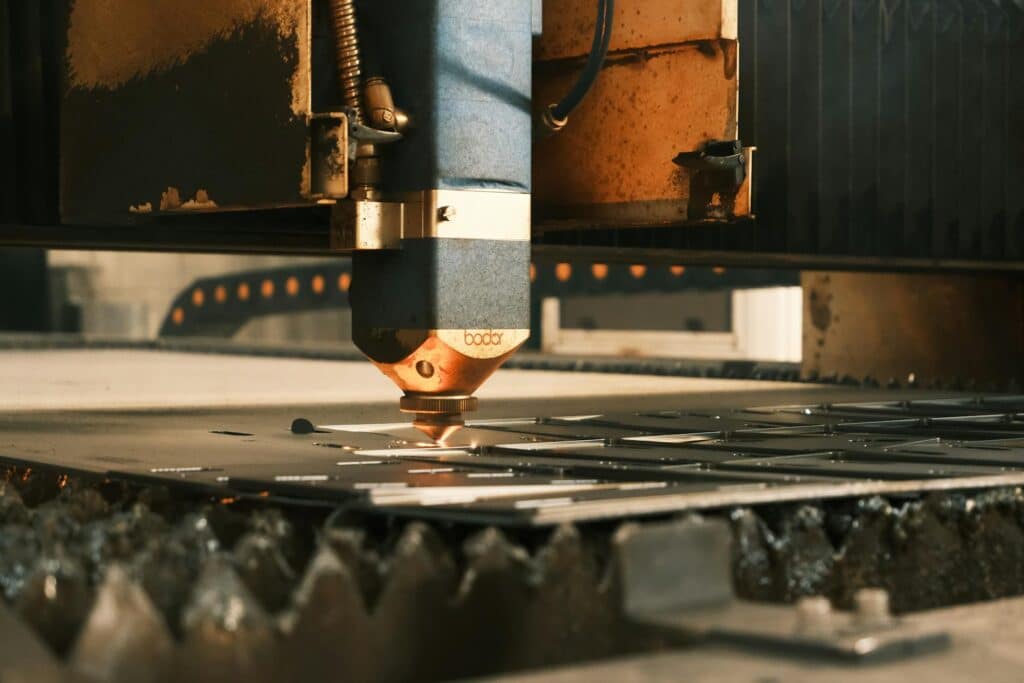
Sage 100 offers multiple manufacturing solutions that streamline various back-end processes and connect disparate workflows, with many of these also going through significant improvements and overhauls in recent years that have revamped the level of functionality available. This includes the launch of newer modules that replaced older versions and introduced additional enhancements over these legacy features.
In this past webinar, the Sage 100 consultant team at SWK Technologies walks through the differences between three of these modules and demonstrates some of their key functionality firsthand. Continue reading below to see a detailed breakdown of these solutions and similar features for manufacturing in your Sage ERP:
The Evolution of Sage 100 Manufacturing
Manufacturers and distributors have seen often precedented levels of change over the 2020’s, from supply chains stretched to the limit to widespread digitization of traditional processes. In response to this disruption and to leverage improvements in technology, Sage has regularly rolled out new upgrades and added improvements for its Sage 100 manufacturing suite, including overhauling aging applications and streamlining connectivity with other systems and cloud-based services. No modern technology stack can be over-reliant on a single system that could become a critical point of failure – integrated databases and workflows are key to keeping pace with the faster pace of the current market.
Sage 100 Bill of Materials – Core Foundation
The Bill of Materials (BOM) module serves as one of the cornerstones for the functionality embedded in Sage 100’s solutions suite for manufacturers, providing a structural framework for tracking and tracing individual product components. Every bill is generated with a description, a category type and detailed list of materials that could include line items, miscellaneous charge codes or comment lines. As each finished product is created and recorded, BOM automatically updates your Inventory Management data to relieve component items or add finished products in.
Here are some of the different types of bills of material that can be produced in your Sage ERP and their features available with the BOM module:
Standard Bills:
- Used in production and work ticket entries
- Support multiple layers of sub-assemblies
- Include component items and miscellaneous charges
- Allow for phantom bills and comment lines
Engineering Bills:
- Support new product structure development
- Enable cost and profitability estimation
- Facilitate engineering change control
- Track revisions and modifications
Kit Bills:
- Define single-level assembled items
- Support component items and comment lines
- Enable streamlined kit processing
- Facilitate sales order processing
Phantom Bills:
- Support interim manufacturing steps
- Enable subassembly management
- Group commonly used components
- Streamline production processes
Sage 100 Production Management – Advanced Controls
Production Management (PM) replaced the legacy Work Order (WO) module in 2019, replicating much of its core order tracking functionality while adding three times as many features, as well as allowing users to create longer and more complex work tickets. This module provides a more end-to-end solution for make-to-stock or make-to-promise manufacturing processes, granting a greater level of visibility into ongoing operations at different stages.
Technical Improvements Over WO:
- Modern Business Framework architecture with enhanced data entry grids
- Extended work ticket numbers (12 digits) and step numbers (6 digits)
- User Defined Fields (UDFs) and Custom Tables
- Crystal Reports integration for all reporting
- Batch data entry capabilities with merge and renumber options
- Real-time inventory updating with subscription service
Process Improvements to WO:
- Work ticket classes for standardizing production settings
- Enhanced labor tracking with punch-in/punch-out functionality
- Quick-release functionality via status changes
- Simplified material and labor back-flushing
- Improved scrap and yield tracking
- Individual promise date tracking for materials
- Direct import capabilities for materials from external files
Cost Management Features:
- Standard cost completion options
- Multiple costing methods (Actual, Standard, Lower of Standard or Actual)
- Original and revised budget maintenance
- Comprehensive totals tab showing budget vs. actual costs by step
- Enhanced overhead calculation options
- Material costing based on Last, Standard, or Average cost
Integration Capabilities:
- Seamless integration with Sage 100 Payroll for labor processing
- Enhanced Purchase Order integration for outside processing
- Improved Bill of Materials integration including revision tracking
- Dynamic Inventory updates with real-time transaction processing
Sage Operations Management (OM) – Custom Manufacturing
Formerly the Sage 100cloud Manufacturing suite, the revamped Operations Management (OM) delivers new comprehensive capabilities for manufacturers specializing in custom or make-to-order production. This module helps you reduce the time spent managing projects and automates manual processes, including generating purchase orders, generating work tickets, checking material availability before release, and verifying quote accuracy and production schedules before production starts.
Manufacturing Process Control:
- Integration with Sales Order for streamlined order processing
- Support for both make-to-stock and make-to-order manufacturing
- Comprehensive job lifecycle management from estimating through delivery
- Real-time work-in-progress visibility and status tracking
- Advanced scheduling and resource allocation tools
Inventory and Materials Management:
- Automated material requirements planning
- Real-time inventory tracking across departments
- Streamlined purchase order generation
- Multi-bin inventory management capabilities
- Automated data collection to eliminate redundant entry
Financial Integration and Analysis:
- Complete integration with Sage 100 accounting functions
- Real-time cost tracking and analysis
- Profitability analysis with remaining cost projections
- Unified financial and operational reporting
- Automated labor and material cost allocation
Advanced Manufacturing Features:
- Product configurator for custom manufacturing
- Real-time capacity confirmation
- Mobile shop floor data collection
- Field service management integration
- Automated workflow management
Sage 100 Inventory Requirements Planning (IRP) – Materials Tracking & Planning
Inventory Requirements Planning (IRP) replaced the legacy Material Requirements Planning (MRP) module, retaining the core reporting functionality while introducing over 10 times as many new features. This solution provides both manufacturers and distributors with demand-based materials tracking and control automations that help you streamline manual inventory planning and work ticket processes.
Planning Capabilities:
- Demand evaluation based on sales orders and production requirements
- Supply analysis through inventory levels and purchase orders
- Integration of build times and lead times
- Real-time planning and decision support
- Interactive dashboard interfaces
- Automated purchase order generation
- Work ticket creation automation
Integration Features:
- Seamless inventory management integration
- Purchase order system connectivity
- Sales order requirement analysis
- Production management coordination
- Comprehensive reporting capabilities
Integration Options
All manufacturing solutions in Sage 100 are designed to work seamlessly together and integrate with other key modules:
Core Integrations:
- Inventory Management
- Purchase Order
- Sales Order
- General Ledger
- Accounts Payable
- Accounts Receivable
Additional Integrations:
- Payroll
- Sage CRM
- Sage Fixed Assets
- Business Intelligence
- Project Management
Choosing the Right Sage 100 Manufacturing Solution
The choice between Production Management and Operations Management depends on your manufacturing approach and business needs:
Production Management
- Make-to-stock manufacturing environments
- Standardized production processes
- High-volume manufacturing
- Businesses focused on inventory optimization
- Companies requiring real-time inventory updates
- Organizations with standard cost accounting needs
Operations Management
- Make-to-order manufacturing
- Custom product manufacturing
- Project-based manufacturing
- Businesses requiring detailed job costing
- Companies with complex scheduling needs
- Organizations requiring product configuration
Both solutions can be enhanced with IRP for comprehensive materials planning and procurement automation, enabling you to optimize inventory levels while ensuring production efficiency.
Learn More About Your Manufacturing Options for Sage ERP
SWK Technologies will help you optimize your manufacturing operations with the right Sage 100 solution, drawing from our extensive experience as a leading Sage partner and manufacturing technology consultant. Review our comprehensive Sage 100 manufacturing resources and guides, and connect with our team of expert consultants to explore which module best fits your production requirements.
Contact SWK here to receive guidance on selecting and implementing the ideal Sage 100 manufacturing solution for your business.